فرآیند تولید سفال: راهنمای جامع و گام به گام از صفر تا صد
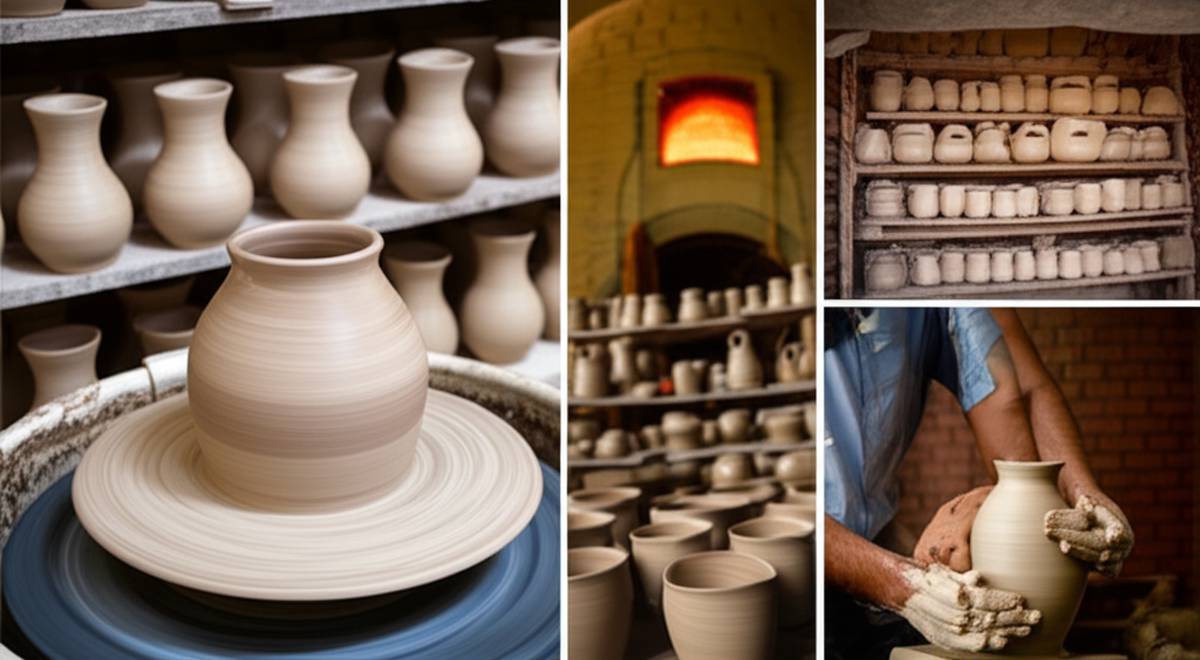
فرآیند تولید سفال
فرآیند تولید سفال، هنر و صنعتی باستانی است که طی آن خاک رس پس از آماده سازی، شکل دهی و قرار گرفتن در معرض حرارت بالا، به محصولی سخت، مقاوم و زیبا تبدیل می شود. این دگرگونی شگفت انگیز خاک، از هزاران سال پیش تاکنون، زندگی بشر را با ظروف کاربردی و اشیاء هنری عجین کرده است.
سفال، ماده ای است که از دوران باستان تا به امروز، همواره نقشی اساسی در زندگی بشر ایفا کرده است. این ماده کهن و پرکاربرد، حاصل دست های هنرمند انسان و طبیعت سخاوتمند است که از دل خاک برمی خیزد و با گذشتن از مراحل پیچیده و دقیق، به اشیایی مقاوم و مفید تبدیل می شود. درک فرآیند تولید سفال نه تنها برای متخصصان و دانشجویان رشته های مرتبط ارزشمند است، بلکه برای هر علاقه مندی که شیفته هنر و صنعت دیرینه سفالگری است، دریچه ای نو به سوی این دنیای جذاب می گشاید. این فرآیند، داستانی از صبر، دقت و دگرگونی است که هر مرحله آن، نیازمند دانش و تجربه خاصی است. در این مقاله، سفری جامع به مراحل گوناگون تولید سفال، از انتخاب مواد اولیه تا رسیدن به محصول نهایی، خواهیم داشت و ابعاد مختلف این هنر-صنعت را بررسی خواهیم کرد.
سفال چیست؟ هنر و صنعت دیرینه خاک و آتش
سفال به هر محصولی گفته می شود که از خاک رس ساخته شده و پس از شکل دهی، در دمای بالا پخته شده باشد. این محصولات طیف وسیعی از اشیاء را شامل می شوند، از ظروف کاربردی و کاشی های تزیینی گرفته تا مصالح ساختمانی مانند آجر و بلوک های سفالی. تفاوت اصلی سفال با سرامیک در نوع خاک رس مورد استفاده و دمای پخت است. سفال ها معمولاً از خاک رس با ناخالصی های بیشتر و در دماهای پایین تر (معمولاً زیر ۱۱۰۰ درجه سانتی گراد) پخته می شوند، در حالی که سرامیک ها از خاک های خالص تر (مانند کائولن) و در دماهای بسیار بالاتر تولید می شوند که منجر به ساختاری متراکم تر و آب گریزتر می شود.
تاریخچه سفالگری به دوران نوسنگی و آغاز استقرار بشر و کشاورزی بازمی گردد، جایی که نیاز به نگهداری مواد غذایی و آب، انسان را به سمت ساخت ظروف سفالی سوق داد. قدیمی ترین شواهد سفالگری به حدود ۲۹۰۰۰ سال پیش در جمهوری چک بازمی گردد. از آن زمان به بعد، سفالگری به سرعت در فرهنگ های مختلف جهان گسترش یافت و در هر منطقه، با ویژگی های بومی و هنری خاص خود شکوفا شد. سفال به دلیل خواص منحصربه فردی همچون عایق بودن در برابر حرارت و صوت، مقاومت نسبی در برابر فشار و ضربه، و قابلیت شکل پذیری بالا، همواره مورد توجه بوده است. شکل پذیری خاک رس به هنرمندان اجازه می دهد تا بی نهایت طرح و فرم را خلق کنند، در حالی که فرآیند پخت، این اشکال را به ساختارهایی پایدار و بادوام تبدیل می کند.
امروزه کاربردهای سفال فراتر از ظروف ساده آشپزخانه رفته و در حوزه های متنوعی از جمله معماری (کاشی، آجر، بلوک های ساختمانی)، دکوراسیون داخلی و خارجی، صنایع دستی و هنرهای زیبا حضوری پررنگ دارد. آجر و بلوک های سفالی، به دلیل سبکی و خواص عایق بندی، از پرکاربردترین مصالح در صنعت ساختمان سازی هستند و به بهینه سازی مصرف انرژی در ساختمان ها کمک می کنند. همچنین، ظروف سفالی لعاب دار، علاوه بر زیبایی، به دلیل مقاومت در برابر رطوبت و سهولت تمیزکاری، همچنان جایگاه ویژه ای در خانه ها دارند.
مواد اولیه اساسی در ساخت سفال
پایه و اساس هر اثر سفالی، از ظریف ترین گلدان ها تا مستحکم ترین آجرها، به مواد اولیه آن بازمی گردد. درک دقیق خواص و نقش هر یک از این مواد، کلید تولید سفالی باکیفیت و دوام بالاست.
خاک رس: بستر اصلی خلاقیت
خاک رس، قلب تپنده فرآیند سفالگری است. این ماده طبیعی که از فرسایش سنگ های آذرین و دگرگونی در طی میلیون ها سال شکل گرفته، به دلیل ساختار صفحه ای و ریزدانه اش، خاصیت شکل پذیری بی نظیری دارد. وقتی آب به خاک رس اضافه می شود، ذرات صفحه ای آن روی یکدیگر می لغزند و به گل حالتی پلاستیکی می دهند که می توان آن را به راحتی شکل داد.
انواع مختلفی از خاک رس برای سفالگری استفاده می شوند که هر یک ویژگی های خاص خود را دارند:
-
کائولین: خاکی خالص، سفید و دیرگداز که عمدتاً در تولید چینی و سرامیک های ظریف به کار می رود. خاصیت شکل پذیری کمتری دارد.
-
بال کلی (Ball Clay): خاکی بسیار پلاستیک با رنگ تیره که به تنهایی برای ساخت سفال استفاده نمی شود اما برای افزایش خاصیت شکل پذیری به کائولین یا خاک های دیگر اضافه می شود.
-
فایرکلی (Fireclay): خاکی مقاوم به حرارت بالا که در تولید آجر نسوز و محصولات صنعتی به کار می رود.
-
خاک رس معمولی: متداول ترین نوع خاک رس که به دلیل فراوانی و خواص شکل پذیری مناسب، در تولید سفال های سنتی، آجر، و کاشی استفاده می شود. این خاک ها معمولاً حاوی ناخالصی هایی مانند اکسید آهن هستند که پس از پخت، رنگی قرمز یا نارنجی به محصول می دهند.
خواص فیزیکی و شیمیایی خاک رس، مانند اندازه ذرات، میزان ناخالصی ها، و ترکیب شیمیایی، مستقیماً بر خواص محصول نهایی (مانند میزان انقباض در حین خشک شدن و پخت، رنگ پذیری و مقاومت) تأثیر می گذارد. انتخاب خاک رس با کیفیت، اولین گام برای اطمینان از دوام و زیبایی سفال است.
آب: عنصر شکل دهنده حیات
آب، عنصری حیاتی در فرآیند تولید سفال است. این مایع نه تنها به خاک رس خاصیت شکل پذیری می بخشد، بلکه در مراحل آماده سازی گل، به همگن سازی ذرات و حذف حباب های هوا نیز کمک می کند. مقدار آب مورد نیاز به نوع خاک رس و روش شکل دهی بستگی دارد. آب بیش از حد، گل را شل و غیرقابل کنترل می کند و آب کم، گل را سفت و شکننده می سازد. یافتن تعادل مناسب، هنر و تجربه خاص خود را می طلبد تا خمیری با قوام مطلوب به دست آید که بتواند به بهترین شکل ممکن فرم گیرد.
افزودنی ها و اصلاح کننده ها
در برخی موارد، برای بهبود خواص خاک رس یا افزایش کارایی فرآیند تولید، مواد افزودنی به گل سفالگری اضافه می شوند. این افزودنی ها می توانند ویژگی های متعددی از جمله خاصیت شکل پذیری، مقاومت در برابر حرارت، رنگ، یا میزان انقباض را تحت تأثیر قرار دهند.
-
ماسه یا سیلیس: برای کاهش انقباض و ترک خوردگی در حین خشک شدن و پخت، و همچنین افزایش مقاومت در برابر شوک حرارتی اضافه می شود.
-
فلدسپات: به عنوان یک کمک ذوب عمل کرده و به کاهش دمای پخت و افزایش تراکم بدنه سفال کمک می کند.
-
مواد آلی: مانند خاک اره یا نشاسته، که برای افزایش تخلخل و سبکی محصول به کار می روند، به خصوص در تولید آجرهای سبک یا بلوک های سفالی فوم دار.
-
مواد کم کننده انقباض: پودرهای خاصی که برای کنترل ابعاد و جلوگیری از تغییر شکل بیش از حد محصولات در حین پخت استفاده می شوند.
ترکیب دقیق این افزودنی ها با خاک رس، با توجه به نوع محصول نهایی و خواص مطلوب آن، تعیین می شود و نیازمند دانش فنی و آزمایش های دقیق است.
مراحل گام به گام فرآیند تولید سفال: از گل تا گنجینه
فرآیند تولید سفال، مجموعه ای از مراحل دقیق و پیوسته است که هر یک نقش حیاتی در کیفیت و دوام محصول نهایی دارند. این سفر از دل خاک آغاز می شود و با لمس حرارت آتش به کمال می رسد.
آماده سازی مواد اولیه: زیربنای کیفیت
اولین گام در فرآیند تولید سفال، آماده سازی خاک رس است. این مرحله تضمین کننده خلوص و یکنواختی ماده اولیه است و تأثیر مستقیمی بر کیفیت نهایی محصول دارد.
-
استخراج و انتقال: خاک رس از معادن مخصوص استخراج شده و به کارخانه های تولید سفال یا کارگاه های سفالگری منتقل می شود.
-
شستشو و خالص سازی: خاک رس خام معمولاً حاوی ناخالصی هایی مانند سنگ، ریشه گیاهان، شن، و مواد آلی است. برای حذف این ناخالصی ها، خاک رس را با آب مخلوط کرده و سپس از فیلترها و صافی های مخصوص عبور می دهند. این کار به افزایش خلوص و همگن شدن خاک کمک می کند. در روش های صنعتی، این فرآیند اغلب با دستگاه های پیشرفته انجام می شود.
-
خشک کردن اولیه: پس از شستشو، خاک رس دارای رطوبت زیادی است. برای سهولت در فرآیندهای بعدی مانند خردایش، خاک را تا حدی خشک می کنند. این خشک کردن می تواند در هوای آزاد یا با استفاده از خشک کن های صنعتی انجام شود.
-
خردایش و آسیاب کردن: خاک رس خشک شده به قطعات کوچک تر خرد شده و سپس در آسیاب های مخصوص به پودری یکنواخت و نرم تبدیل می شود. اندازه ذرات باید به دقت کنترل شود تا محصول نهایی دارای بافت مطلوب و بدون ناهمگونی باشد.
-
الک کردن: پودر خاک رس آسیاب شده از الک های با مش بندی مختلف عبور داده می شود تا ذرات درشت تر جدا شده و یکنواختی نهایی حاصل شود. این کار به بهبود کیفیت سطح و کاهش عیوب احتمالی کمک می کند.
-
افزودن آب و ورز دادن: در این مرحله، آب به پودر خاک رس اضافه شده و مخلوط می شود تا گل سفالگری یا دوغاب (بسته به روش شکل دهی) به دست آید. ورز دادن (Kneading یا Pugging) یکی از مهمترین مراحل است. در این مرحله، گل بارها فشرده و کشیده می شود تا حباب های هوای محبوس در آن خارج شده و گل کاملاً همگن و پلاستیک شود. حذف حباب های هوا برای جلوگیری از ترک خوردگی و انفجار محصول در کوره بسیار حیاتی است.
شکل دهی و قالب گیری: تجلی فرم
پس از آماده سازی گل، نوبت به مرحله شکل دهی می رسد، جایی که ماده خام به فرم دلخواه تبدیل می شود. روش های مختلفی برای شکل دهی وجود دارد که بسته به نوع محصول و مقیاس تولید انتخاب می شوند.
روش های دستی و سنتی
در این روش ها، مهارت و هنر سفالگر نقش اصلی را ایفا می کند:
-
چرخ سفالگری (کوزه گری): یکی از قدیمی ترین و هنری ترین روش هاست. سفالگر گل را روی چرخ گردان قرار داده و با استفاده از دست ها و ابزار مخصوص، با نیروی چرخشی و مهارت خود، آن را به اشکال مختلف (مانند کوزه، کاسه، گلدان) تبدیل می کند. این روش بیشتر برای ظروف متقارن و دایره ای شکل مناسب است.
-
ساخت با دست (Hand-building): این روش شامل تکنیک های مختلفی است که بدون استفاده از چرخ انجام می شود:
- تکنیک کویل (Coil): گل به صورت طناب های بلند درآمده و روی هم قرار می گیرد تا فرم دلخواه ایجاد شود.
- تکنیک ورقه (Slab): گل به صورت ورقه های مسطح پهن شده و سپس برش خورده و به هم چسبانده می شود تا اشکال هندسی یا غیرمتقارن ساخته شود.
- تکنیک پینچ (Pinch): با فشردن یک تکه گل با انگشتان، ظرفی ساده و کوچک ساخته می شود.
روش های صنعتی
این روش ها برای تولید انبوه و یکنواخت محصولات سفالی به کار می روند:
-
قالب گیری فشاری (اکستروژن): در این روش، گل با فشار بالا از میان یک قالب (دای) عبور داده می شود تا اشکالی با سطح مقطع ثابت مانند آجر، بلوک، لوله های سفالی یا کاشی های ساده تولید شود. این روش سرعت بالایی دارد و برای تولید مصالح ساختمانی بسیار مناسب است.
-
قالب گیری دوغابی (Slip Casting): برای تولید ظروف پیچیده با دیواره های نازک، مانند چینی بهداشتی یا ظروف پذیرایی، از این روش استفاده می شود. دوغاب رقیق خاک رس در قالب های گچی ریخته می شود. گچ، آب دوغاب را به خود جذب کرده و لایه ای از گل جامد روی سطح داخلی قالب تشکیل می شود. پس از خشک شدن، محصول از قالب خارج می شود.
-
قالب گیری پرسی (Pressing): این روش برای تولید کاشی و سرامیک استفاده می شود. پودر خاک رس با رطوبت کم، تحت فشار بالا در قالب های فلزی فشرده می شود تا به شکل دلخواه درآید. این روش دقت ابعادی بالایی دارد.
پس از شکل دهی، به ویژه در روش های صنعتی مانند اکستروژن برای آجر و بلوک، محصولات به ابعاد مورد نظر برش می خورند تا برای مراحل بعدی آماده شوند.
خشک کردن اولیه (خشت): استراحت پیش از آتش
پس از شکل دهی، محصولات سفالی که در این مرحله خشت نامیده می شوند، حاوی مقادیر زیادی آب هستند. خشک کردن یکی از حساس ترین مراحل است، زیرا آب باید به آرامی و به صورت یکنواخت از خشت خارج شود تا از ترک خوردگی، تاب برداشتن یا اعوجاج جلوگیری شود. اگر خشک کردن با سرعت زیاد انجام شود، سطح خشت سریع تر خشک شده و منقبض می شود، در حالی که قسمت های داخلی هنوز مرطوب و متورم هستند، که این اختلاف منجر به ترک خوردگی خواهد شد.
روش های خشک کردن عبارتند از:
-
خشک کردن هوایی: در کارگاه های سنتی، خشت ها در محیطی با تهویه مناسب و دور از تابش مستقیم آفتاب قرار می گیرند تا به آرامی خشک شوند. این روش زمان بر است اما کمترین ریسک ترک خوردگی را دارد.
-
اتاق های خشک کن: در مقیاس صنعتی، از اتاق های خشک کن با کنترل دما و رطوبت استفاده می شود. این اتاق ها شرایط بهینه را برای خشک شدن یکنواخت فراهم می کنند.
-
خشک کن های تونلی: در کارخانه های بزرگ، خشت ها از داخل تونل های طولانی عبور داده می شوند که در طول آن دما و رطوبت به تدریج تغییر می کند تا فرآیند خشک شدن به صورت کنترل شده و سریع تر انجام شود.
هدف از این مرحله، کاهش رطوبت خشت تا حدی است که محصول از استحکام کافی برخوردار شود و برای پخت اولیه آماده باشد، اما همچنان مقداری رطوبت شیمیایی در ساختار آن باقی می ماند که در مرحله پخت آزاد می شود.
پخت اولیه (بیسکویت یا بیسک فایر): آغاز دگرگونی
خشت های خشک شده وارد مرحله پخت اولیه می شوند که به آن بیسکویت فایر یا بیسک فایر نیز گفته می شود. هدف از این پخت، افزایش استحکام مکانیکی خشت، کاهش شکنندگی آن، و آماده سازی برای مرحله لعاب زنی است. در این مرحله، خشت در دمای نسبتاً پایین (معمولاً بین ۸۰۰ تا ۱۰۰۰ درجه سانتی گراد) پخته می شود.
تغییرات فیزیکی و شیمیایی مهمی در این مرحله رخ می دهد:
-
از دست دادن آب شیمیایی: آبی که به صورت شیمیایی در ساختار خاک رس وجود دارد، در این دما از بین می رود.
-
سخت شدن: ذرات خاک رس به یکدیگر متصل می شوند و ساختار متراکم تر و مقاوم تری پیدا می کنند، اما هنوز کاملاً متراکم نشده اند و دارای تخلخل هستند. این تخلخل باعث می شود که خشت آماده جذب لعاب باشد.
-
آماده سازی برای لعاب زنی: استحکام حاصل از بیسکویت فایر، به سفالگر اجازه می دهد تا محصول را بدون نگرانی از آسیب دیدن، لعاب زنی کند. همچنین تخلخل بدنه، لعاب را به خوبی جذب می کند.
دمای پخت اولیه و مدت زمان آن باید به دقت کنترل شود تا از تغییر شکل یا ترک خوردگی محصول جلوگیری شود.
لعاب زنی (مرحله اختیاری): رخت زیبایی و محافظت
لعاب زنی مرحله ای اختیاری اما بسیار مهم است که به سفال خواصی نظیر زیبایی، نفوذناپذیری، مقاومت در برابر سایش، و محافظت در برابر مواد شیمیایی می بخشد. لعاب، یک پوشش شیشه ای است که روی سطح سفال قرار می گیرد و در اثر حرارت به آن می چسبد.
انواع لعاب ها بر اساس ترکیب شیمیایی و دمای پخت متفاوتی دارند. روش های اعمال لعاب نیز گوناگون است:
-
غوطه وری (Dipping): محصول در حمام لعاب غوطه ور می شود. این روش برای پوشش یکنواخت سطح مناسب است.
-
اسپری کردن (Spraying): لعاب با استفاده از اسپری روی سطح پاشیده می شود. این روش برای پوشش دهی سطوح بزرگ یا اشکال نامنظم کاربرد دارد.
-
نقاشی (Painting) یا قلم مو (Brushing): لعاب با قلم مو روی سفال اعمال می شود که برای ایجاد طرح ها و نقاشی های ظریف مناسب است.
پس از لعاب زنی، محصول باید دوباره خشک شود تا لعاب به خوبی به بدنه بچسبد و برای پخت نهایی آماده شود.
پخت نهایی (لعاب): اوج هنر و مقاومت
مرحله پخت نهایی، که پس از لعاب زنی انجام می شود، اوج فرآیند تولید سفال است. در این مرحله، محصول در دمایی بالاتر (بسته به نوع سفال و لعاب، معمولاً بین ۱۰۵۰ تا ۱۲۵۰ درجه سانتی گراد) پخته می شود. هدف اصلی این پخت، جوش خوردن و ذوب شدن لعاب روی بدنه سفال و تکمیل فرآیند سخت شدن و متراکم شدن بدنه است.
کنترل دقیق دما و جو کوره در این مرحله حیاتی است. افزایش دما باید به تدریج انجام شود تا از شوک حرارتی و ترکیدگی جلوگیری شود. پس از رسیدن به دمای اوج و نگهداری برای مدت زمان مشخص، کوره به آرامی سرد می شود. سرد کردن ناگهانی می تواند منجر به ترک خوردگی، شکستگی، یا ایجاد تنش در لعاب و بدنه شود. این فرآیند آهسته، به مولکول های لعاب اجازه می دهد تا به آرامی نظم بگیرند و به یک ساختار شیشه ای پایدار تبدیل شوند که به خوبی به بدنه سفال چسبیده است.
انواع کوره های مورد استفاده در این مرحله عبارتند از:
-
کوره های تونلی: در کارخانه های بزرگ، محصولات از داخل تونل های بلند عبور داده می شوند که دما در طول تونل به تدریج افزایش و سپس کاهش می یابد. این کوره ها برای تولید انبوه مناسب هستند.
-
کوره های گردان: این کوره ها به صورت استوانه ای هستند که می چرخند و برای پخت محصولاتی مانند سیمان و کلینکر نیز کاربرد دارند.
-
کوره های محفظه ای (Batch Kilns): در این کوره ها، محصولات در یک محفظه قرار گرفته و پس از بارگیری، فرآیند پخت آغاز می شود. این کوره ها انعطاف پذیری بیشتری در کنترل دما و جو دارند و برای تولیدات کمتر یا هنری مناسب هستند.
پس از سرد شدن کامل، محصول سفالی آماده استفاده یا عرضه به بازار است. فرآیند تولید سفال در هر مرحله، نیازمند دقت، تجربه و درک عمیق از رفتار خاک و آتش است. مشاهده این دگرگونی، تجربه ای بی نظیر است که ارزش نهایی سفال را دوچندان می کند.
فرآیند تولید سفال، داستان دگرگونی شگفت انگیز خاک است؛ از توده ای نرم و بی شکل تا اثری هنری و مقاوم که در برابر زمان ایستادگی می کند و قصه ها از دل آن بیرون می آید.
روش های تولید سفال: از کارگاه دستی تا کارخانه عظیم
تولید سفال در طول تاریخ و با پیشرفت تکنولوژی، دستخوش تغییرات زیادی شده است. امروزه، سه رویکرد اصلی برای تولید سفال وجود دارد که هر یک مزایا و محدودیت های خاص خود را دارند.
روش سنتی: لمس دست و روح هنر
در روش سنتی، تمامی مراحل تولید، از استخراج خاک تا پخت نهایی، عمدتاً با دخالت نیروی انسانی و ابزارهای ساده انجام می شود. خاک رس معمولاً به صورت دستی یا با ابزارهای ابتدایی از معادن استخراج شده، ناخالصی ها به روش های دستی جدا می شوند و گل سفالگری با پا یا دست ورز داده می شود. شکل دهی نیز اغلب با چرخ سفالگری دستی یا تکنیک های ساخت با دست صورت می گیرد.
خشک کردن محصولات در این روش معمولاً در هوای آزاد یا در سایه انجام می شود و پخت در کوره های سنتی (مانند کوره های گلی یا هیزمی) که کنترل دما در آن ها دشوارتر است، صورت می پذیرد.
مزایا:
- اصالت هنری و روح صنعتگر در محصول نهایی منعکس می شود.
- قابلیت انعطاف پذیری بالا در طراحی و تولید اشکال منحصربه فرد و سفارشی.
- وابستگی کمتر به ماشین آلات پیچیده و سرمایه گذاری اولیه کمتر.
معایب:
- سرعت تولید بسیار پایین و حجم تولید محدود.
- کیفیت محصول نهایی ممکن است نامنظم باشد (تغییر در ابعاد، استحکام و رنگ).
- نیاز به نیروی کار ماهر و زمان بر بودن فرآیند.
این روش امروزه بیشتر در کارگاه های هنری، آموزشی و برای تولید محصولات خاص و دست ساز کاربرد دارد.
روش نیمه صنعتی: تلفیق سنت و مدرنیته
روش نیمه صنعتی، ترکیبی از دخالت نیروی انسانی و استفاده از ماشین آلات در مراحل خاصی از تولید است. به عنوان مثال، ممکن است آماده سازی خاک رس و ورز دادن آن با ماشین آلات انجام شود، اما قالب گیری یا شکل دهی همچنان به صورت دستی یا با استفاده از چرخ های برقی صورت پذیرد. خشک کردن نیز می تواند در خشک کن های هوایی کنترل شده یا با کمک نور آفتاب انجام شود. پخت ممکن است در کوره های صنعتی کوچک تر یا نیمه اتوماتیک صورت گیرد که کنترل دما در آن ها تا حدی بهبود یافته است.
بسیاری از کارخانه های تولید آجر سفال داخلی در ایران از این روش استفاده می کنند؛ جایی که مراحل اولیه و پخت با ماشین انجام می شود، اما خشک کردن محصول زیر نور آفتاب صورت می گیرد.
ویژگی ها و کاربردها:
- افزایش سرعت تولید نسبت به روش سنتی.
- کیفیت یکنواخت تر محصول نهایی نسبت به روش دستی.
- نیاز به سرمایه گذاری متوسط.
- مناسب برای تولیدات در مقیاس متوسط مانند برخی کارگاه های تولید آجر، کاشی یا ظروف سفالی خاص.
روش تمام اتوماتیک (صنعتی): دقت و سرعت در مقیاس انبوه
در روش تمام اتوماتیک یا صنعتی، تمامی مراحل فرآیند تولید سفال، از آماده سازی مواد اولیه تا بسته بندی محصول نهایی، به صورت کاملاً ماشینی و خودکار و با حداقل دخالت نیروی انسانی انجام می شود. این روش برای تولید انبوه و با کیفیت یکنواخت محصولات سفالی و سرامیکی، به ویژه مصالح ساختمانی، طراحی شده است.
ماشین آلات پیشرفته ای برای خردایش، آسیاب، مخلوط کردن، ورز دادن، شکل دهی (اکسترودر، پرس های هیدرولیک)، خشک کردن (خشک کن های تونلی)، لعاب زنی (ربات های اسپری) و پخت (کوره های تونلی با کنترل دقیق دما و جو) به کار می روند. حتی جابجایی محصولات بین مراحل نیز توسط ربات ها یا نوار نقاله ها صورت می گیرد.
یکی از روش های پیشرفته در تولید آجرهای پلاک نما، روش خشک (Dry Method) است. در این روش، خاک خشک بدون افزودن آب زیاد، مستقیماً در قالب های تحت فشار بالا فشرده می شود و سپس به کوره می رود. این آجرهای فشرده و بدون رطوبت بالا، پس از پخت با سرد شدن تدریجی، مقاومت و دقت ابعادی بالایی پیدا می کنند.
مزایا:
- سرعت تولید بسیار بالا و امکان تولید در مقیاس انبوه.
- کیفیت یکنواخت و استاندارد بالای محصولات.
- دقت ابعادی بالا و کاهش عیوب تولید.
- کاهش هزینه های نیروی کار در بلندمدت.
معایب:
- نیاز به سرمایه گذاری اولیه بسیار زیاد برای خرید ماشین آلات و احداث کارخانه.
- انعطاف پذیری کمتر در تولید محصولات متنوع و سفارشی.
- مصرف بالای انرژی.
هر یک از این روش ها جایگاه خاص خود را در صنعت سفالگری دارند و انتخاب آن ها بستگی به نوع محصول، حجم تولید مورد نظر و سرمایه گذاری در دسترس دارد.
تضمین کیفیت و رفع چالش ها در تولید سفال
کنترل کیفیت در هر مرحله از فرآیند تولید سفال، از انتخاب خاک رس تا پخت نهایی، از اهمیت بالایی برخوردار است. این نظارت دقیق، تضمین کننده دوام، کارایی و زیبایی محصول نهایی خواهد بود. برای سنجش کیفیت، شاخص های کلیدی متعددی بررسی می شوند.
شاخص های کلیدی کیفیت:
- مقاومت فشاری: توانایی محصول در تحمل بارهای فشاری، به ویژه برای مصالح ساختمانی مانند آجر و بلوک.
- جذب آب: میزان آبی که محصول پس از پخت می تواند جذب کند. جذب آب بالا می تواند به کاهش مقاومت و دوام محصول منجر شود، به خصوص در مناطق مرطوب و سرد.
- ابعاد استاندارد: حفظ ابعاد دقیق و یکنواخت برای سهولت در اجرا و زیبایی ظاهری.
- رنگ و بافت: یکنواختی رنگ و بافت سطح محصول، به ویژه برای ظروف تزیینی و کاشی ها.
- سلامت ساختاری: بررسی عدم وجود ترک، حباب، یا سایر ناخالصی ها در بدنه.
با این حال، حتی با وجود کنترل های دقیق، ممکن است عیوبی در محصولات سفالی ظاهر شوند که آگاهی از دلایل آن ها به پیشگیری کمک می کند.
عیوب رایج در محصولات سفالی و دلایل بروز آن ها:
-
ترک خوردگی: می تواند ناشی از خشک شدن ناهموار، ورز دادن ناکافی (وجود حباب هوا)، تغییرات ناگهانی دما در کوره (شوک حرارتی)، یا خاک رس نامناسب باشد.
-
تاب برداشتن (Warping): معمولاً به دلیل خشک شدن نامتقارن، پخت با دمای نامناسب یا پشتیبانی ناکافی از محصول در کوره رخ می دهد.
-
پوک شدن یا متخلخل شدن بیش از حد: ناشی از دمای پخت پایین تر از حد لازم، یا وجود ناخالصی های آلی در خاک که در حین پخت می سوزند و فضای خالی ایجاد می کنند. این عیب، مقاومت محصول را کاهش می دهد.
-
تغییر رنگ ناخواسته: ممکن است به دلیل وجود ناخالصی های معدنی در خاک رس، جو نامناسب کوره (اکسیدی یا احیایی)، یا پخت در دمای نادرست باشد.
-
لعاب پریدگی یا ترک خوردن لعاب (Crazing/Shivering): معمولاً به دلیل عدم تطابق ضریب انبساط حرارتی لعاب و بدنه سفال رخ می دهد. همچنین می تواند ناشی از پخت نامناسب لعاب یا ضخامت نامناسب آن باشد.
شناسایی و تحلیل این عیوب، قدمی مهم در بهبود مستمر فرآیند تولید و ارتقاء کیفیت محصولات سفالی است. با نظارت مستمر و اعمال دانش فنی، می توان بسیاری از این مشکلات را به حداقل رساند و محصولاتی با دوام و مطلوب به بازار عرضه کرد.
نگاهی دقیق تر به فرآیند تولید آجر سفال
آجر سفال، به عنوان یکی از مهمترین مصالح ساختمانی، نقشی حیاتی در پایداری و عایق بندی ساختمان ها دارد. فرآیند تولید آن، با تفاوت هایی جزئی، از همان اصول کلی سفالگری پیروی می کند، اما با تمرکز بر تولید انبوه و ویژگی های سازه ای.
آجر سفال از خاک رس غنی تهیه می شود و پس از آماده سازی و قالب گیری، در کوره پخته می شود تا به استحکام و مقاومت لازم برای تحمل بارهای ساختمانی و مقاومت در برابر عوامل محیطی برسد. ویژگی های خاص آجر سفال شامل سبکی (به دلیل حفره های داخلی)، خواص عایق بندی حرارتی و صوتی مناسب، و قیمت اقتصادی آن است که آن را به گزینه ای محبوب در صنعت ساختمان تبدیل کرده است. این حفره ها همچنین به کاهش وزن سازه کمک کرده و سرعت اجرا را بالا می برند.
انواع آجر سفال و کاربردهای آن ها:
-
آجر سفال تیغه ای (بلوک دیواری): این آجرها با ابعاد بزرگ تر و عرض کمتر، عمدتاً برای ساخت دیوارهای جداکننده داخلی و دیوارهای غیرباربر استفاده می شوند. هدف اصلی آن ها تقسیم فضا و ایجاد عایق صوتی و حرارتی است.
-
آجر سفال سقفی: این نوع بلوک ها سبک وزن هستند و برای استفاده در سقف های تیرچه بلوک طراحی شده اند. آن ها فضای خالی بین تیرچه ها را پر می کنند و به عایق بندی سقف کمک می کنند.
-
آجر سفال نما: این آجرها با ظاهری زیبا و سطحی یکنواخت، برای استفاده در نمای خارجی ساختمان ها به کار می روند. آن ها معمولاً در رنگ ها و طرح های متنوع تولید می شوند.
-
آجر سفال فوم دار: این آجرها با افزودن فوم یا مواد آلی به ترکیب خاک رس تولید می شوند که پس از پخت می سوزند و حفرات ریز ایجاد می کنند. این فرآیند باعث افزایش خواص عایق بندی حرارتی و صوتی و کاهش وزن آجر می شود.
-
آجر مجوف دیواری: منظور همان آجرهای مکعب مستطیل دارای سوراخ هستند که در ابعاد و اندازه های مختلف تولید می شوند و برای ایجاد دیوارهای با وزن کمتر و عایق تر به کار می روند.
ابعاد رایج بلوک های سفالی:
ابعاد بلوک های سفالی متناسب با کاربردشان متفاوت است. معمولاً این بلوک ها در ضخامت های ۷، ۱۰، ۱۵ و ۲۰ سانتی متری و طول و عرض های استاندارد (مانند ۲۰x۲۰x۴۰ یا ۲۰x۲۵x۶۰ سانتی متر) تولید می شوند که هر کدام برای تیغه بندی، دیوارچینی یا سقف مناسب هستند.
مقایسه مختصر آجر سفال با سایر بلوک های ساختمانی:
ویژگی | آجر سفال | بلوک سبک (هبلکس / AAC) | بلوک لیکا |
---|---|---|---|
وزن | سبک (نسبت به آجر سنتی) اما سنگین تر از بلوک های سبک | بسیار سبک | سبک (مابین سفال و هبلکس) |
سرعت اجرا | متوسط | بالا (به دلیل ابعاد بزرگتر و چسب مخصوص) | بالا (به دلیل ابعاد بزرگتر) |
عایق بندی حرارتی | متوسط | بسیار خوب | خوب |
عایق بندی صوتی | متوسط | بسیار خوب | خوب |
مقاومت فشاری | خوب | متوسط تا خوب | خوب |
مصالح چسباننده | ملات ماسه سیمان | چسب بلوک مخصوص | ملات ماسه سیمان یا چسب لیکا |
ترک در گچ کاری | احتمال ترک خوردگی سطح گچ | احتمال کمتر | احتمال کمتر |
آجر سفال به دلیل سبکی و قیمت مناسب، همچنان یکی از گزینه های پرکاربرد در صنعت ساختمان سازی است، به ویژه برای دیوارهای غیرباربر و تیغه بندی ها. اما انتخاب نوع بلوک، به نیازهای پروژه، بودجه و اولویت های مهندسی بستگی دارد.
نتیجه گیری
فرآیند تولید سفال، با تمام پیچیدگی ها و جزئیاتش، گواهی بر خلاقیت و هوشمندی انسان در بهره گیری از منابع طبیعی است. از لمس خاک رس نرم و پلاستیکی تا تماشای دگرگونی آن در کوره های آتشین، هر مرحله داستانی از صبر و علم را روایت می کند. سفالگری، نه تنها یک صنعت حیاتی برای تأمین نیازهای بشر بوده، بلکه همواره هنری الهام بخش برای روح جستجوگر انسان باقی مانده است.
درک این فرآیند، اهمیت کنترل کیفیت در هر گام را نمایان می سازد، از انتخاب دقیق خاک گرفته تا نظارت بر دمای پخت و سرد کردن تدریجی. هر نقص کوچکی در این زنجیره می تواند به محصول نهایی آسیب برساند و تلاش های بسیار را بی ثمر کند. سفال، با کاربردهای متنوع خود در زندگی روزمره و صنعت، از ظروف ساده آشپزخانه تا مصالح ساختمانی مقاوم، همواره حضوری پررنگ داشته و نقشی حیاتی در توسعه و فرهنگ بشری ایفا کرده است.
با پیشرفت تکنولوژی، آینده سفالگری نیز شاهد نوآوری های بیشتری خواهد بود، از روش های تولید خودکارتر تا توسعه مواد اولیه جدید و پایدارتر. اما در هر رویکردی، روح اصیل این هنر کهن که از خاک و آتش جان می گیرد، همچنان زنده و پویا باقی خواهد ماند و این فرآیند، پیوسته به ما یادآوری می کند که چگونه می توان با کمی دانش و تجربه، از دل سادگی، زیبایی و دوام آفرید.