نحوه تولید سیم مفتول چگونه است؟
توسعه و کاربرد عملی فناوری نورد پیوسته:
در تولید مفتول نورد مفتول فرآیندی است که طولانیترین عمر عملیاتی را در بین کارخانههای تولیدی را در حال حاضر دارد. ژاپن در طول بهره برداری از نورد، باعث افزایش کیفیت و بهرهوری شده و همچنان به کیفیت و بهرهوری در سطح بالایی توجه میکند.
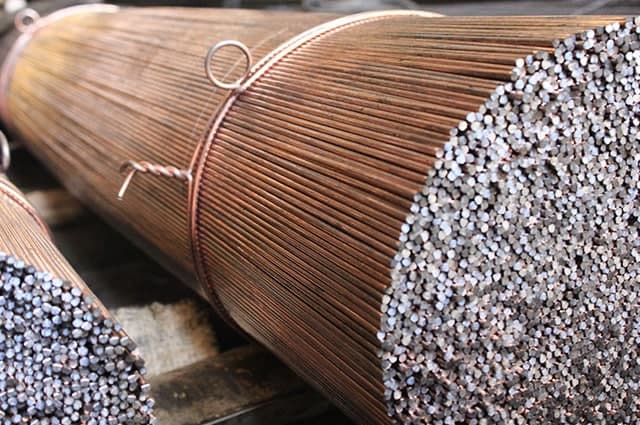
در حال حاضر، کارخانه تولید مفتول بهعنوان یک نورد چندمرحلهای در حال بهره برداری است، و فولادهای مفتولی باکیفیت بالا که توسط و با استفاده از نورد سرد باراندمان بالا تولید میشود. نورد پیوسته برای اولین بار در جهان به نورد چندمرحلهای معرفی شد که برای بهبود عملکرد و بهرهوری و افزایش آزادی در انتخاب وزن واحد کلاف مفتول در نظر گرفته شده بود. جزئیات این فناوری در این بخش معرفیشده است.
4.1 پیش زمینه:
در نورد مفتول، شمش بهطور مداوم به اندازههای تعیین شده از طریق 28 ایستگاه نورد میچرخند. قسمت انتهایی یک شمش در طول خط و بعد از چرخش باید برش داده شده و برداشته شود تا از بروز مشکلات نورد به دلیل شکل ناقص جلوگیری کرده و قسمت کنترل نشده با درجه حرارت ناپایدار را از خط نورد کنار گذاشته میشود.
علاوه بر این، برای کنترل عملکرد نورد باید فاصله خاصی بین انتهای شمشها باشد. این عوامل منجر به ضررهای ناگزیر در بازده و بهرهوری میشود. همچنین در نورد مفتول سیم، کلافهای یک تنی یا دو تنی از شمشهای دو تنی تولید میشوند. با این حال، در روند تولید مفتول مانند تولیدکننده سیم فولادی نرم برای بهبود بهرهوری خود نیاز به افزایش واحد کلاف ساز دارند.
برای به دست آوردن پیشرفت در عملکرد، بهرهوری، و افزایش آزادی انتخاب وزن کلاف، توسعه فناوری نورد پیوسته آغاز شد که در آن شمشها بهصورت خطی به یکدیگر جوش داده میشوند و بهطور مداوم نورد میشوند.
ازآنجاییکه کارخانه سیم مفتول کارخانه، کارخانه چندمرحلهای است و از جنس فولاد باکیفیت بالا بهطور عمده مفتول فولادی تولید میکند، ساخت سیستم اتصال بین شمشها به جوشکاری و فناوری جدید نیاز دارد تا با توسعه کیفیت بخش جوشکاری و افزایش کیفیت محصول، مفتول نهایی از نظر تجاری قابل قبول باشد و این هدف با یک عملیات نورد پیوسته، تنها در بین کارخانههای نورد چندمرحلهای در جهان، تحقق یافته است. در زیر شما مجموعه ماشین کلاف کننده مفتول را مشاهده میکنید.
4.2 کلیه تجهیزات
شکل 9 چیدمان نورد مفتول را نشان میدهد. دستگاه اتصال نورد بین کوره گرمایش و نورد پرفشار نصب میشود و غلتکهای گیرهای قبل و بعد از ماشین اتصال نصب میشوند. در نورد معمولی، همیشه یک فاصله ثابت بین شمش با تنظیم زمان استخراج شمش در کنترل سه بعدی کوره گرمایش و / یا با تنظیم سرعت انتقال غلتکهای گیرهای قبل و بعد از دستگاه اتصال در کنترل متوالی از نورد پرفشار در نظر گرفته میشود.
از طرف دیگر، برای پیوستن شمشها در نورد پیوسته، سرعت انتقال شمش توسط رولهای گیرهای در کناره و جلو کنترل میشود. سپس، سرعت دستگاه اتصال با سرعت انتقال شمش هماهنگ میشود و جوش دادن و اتصال بر روی انتهای شمش با دقت اعمال میشود.
با توجه به توسعه فناوری، اتصال دو شمش بدون کاهش سرعت نورد محقق شد. علاوه بر این، برای تکمیل جوشکاری در یک فضای محدود بین کوره گرمایش و نورد پرفشار، روش جوشکاری فلش لب به لب استفاده شده و جوشکاری در مدت زمان کمی اجراشده است.
پس از اتمام اتصالات، خط جوش و پلیسه تولید شده در قسمت جوشکاری توسط دستگاه پولیش برداشته میشود. پس از نورد، قسمت اتصال به جوش ردیابی میشود و مفتول در بخش اصلاح برش داده میشود تا یک کلاف با وزن مقرر تهیه شود. کل سری عملیات فوق بهصورت خودکار انجام میشود و نورد پیوسته بدون افزایش فشار کاربر اپراتورها محقق شده است.
ویژگیهای نورد پیوسته
4.3.1 کاربرد در کارخانه چندمرحلهای
نورد پیوسته در یک کارخانه تک مرحله قبلاً در شرکتهای مختلفی مورداستفاده قرار گرفته است. با این حال، از آنجا که کارخانه مفتول از نوع نورد چندمرحلهای است، باید ساخت تجهیزات جدید مورد مطالعه قرار گیرد. از آنجا که فضای بین مرحلهها محدود است، نصب یک دستگاه اتصال دهنده بر روی هر مرحله مانند مورد نورد تک مرحلهای دشوار است.
بنابراین، یک دستگاه اتصال که میتواند در سراسر مرحلههای نورد جابجا شده و قابل استفاده در هر مرحلهای از نورد باشد، بهمنظور ایجاد یک دستگاه اتصال میتواند در هر مرحله امکان جوشکاری را ایجاد کند. در طول عملیات اتصال، دستگاه جوشکاری با سرعتی همزمان با سرعت نورد حرکت میکند و پس از اتمام اتصال، دستگاه اتصال به حالت شروع برمی گردد، و در موقعیت اتصال در کنار میایستد تا عملیات جوش بعدی را آغاز کند. با تکرار این چرخه بهره برداری، نورد پیوسته در نورد چندمرحلهای محقق شده است.
شکل 9: نمودار نورد پیوسته مفتول سیمی
شکل 10: نمودار جوشکاری و براده برداری خط خوش شمش شکل 11: شرایط جوش
سایر موضوعاتی که وجود داشت ازجمله وقوع متقابل کنگرهای شدن است که در اتصال و براده برداری خط جوش اتفاق میافتد. روش پیوستن در نورد پیوسته جوشکاری لب به لب است و در حین پیوستن اتصال ایجاد میشود. نگرانی در مورد پلهای شدن شمش باعث ایجاد مشکلات تجهیزات و یا مشکلات کیفیت بر روی مفتول در مرحله مجاور میشود. بنابراین، برای تحقق عملکرد بدون دردسر، لازم است که از کنگره شدن جلوگیری کنید.
برای برطرف کردن این مشکلات و به حداقل رساندن تأثیر کنگره شدن تا حد ممکن، یک حائل برای محصور کردن کنگره شدن شمش و یک دستگاه براده بردار متصل به دیافراگم برای مقابله با کنگره شدن، از نوع دزدگیر بهره برداری شده و این عملکرد اتصال جوش بدون دردسر را محقق کرده است (شکل 10) هر دو دیافراگم حائل و براده بردار بهگونهای طراحی شدهاند که نمیتوانند در عملیات جوشکاری تأثیر بگذارند.
دیافراگم تنها در حین اجرای عملیات پیوستن و جوشکاری فعال میشود و براده بردار بین عملیات پیوستن فعال میشوند. علاوه بر این، هنگامی که برجستگیهای حاصل از جوشکاری در قسمت اتصال تولید میشود، وجود یک ماشین پولیش ضروری است. با این حال، از آنجا که فاصله بین جوشکاری و نورد پرفشار محدود است، تهیه یک دستگاه براده برداری جمع و جور جمع و جور ضروری است.
برای حل این مشکل، یک ماشین ساب با استفاده از نیروی اعمال فشار در نورد و یک ابزار برش توسعه داده شد. علاوه بر این، زمان بندی عملیات پولیش کاری با ردیابی بخش اتصال همزمان میشود.
کاربرد فولاد باکیفیت بال در تولید مفتول
در حال حاضر ساخت بخش جوشکاری برای محصول قابل تولید با فلز درجه تجاری در سایر شرکتهای تولید مفتول عملی شده است. با این حال، از آنجا که کاربرد سیم مفتول برای کاربریهایی با الاستیسیته بالا بیسابقه است، تعیین شرایط جوش از اهمیت حیاتی برخوردار است تا اطمینان حاصل شود که کیفیت بخش متصل شده با جوش بهعنوان کیفیت فرآورده مورد نیاز قابل قبول است.
برای این منظور، قدرت جوشکاری، زمان جوشکاری بر روی تجهیزات واقعی مورد آزمایش قرار میگیرد تا اجسام غیرفلزی قبل از جوشکاری از قسمت خط جوش خارج شود. بنابراین، شرایط جوشکاری فراهم میشود که امکان تولید سیم مفتولی بدون ترک را حتی برای تولید مفتول مورداستفاده در کاربریهای الاستیک روش تولید مفتول
کارخانجات نورد جهت تولید مفتول، شمش مورد نیاز را در کوره های پیش گرم قرار داده و تا رسیدن به دمای 1200 درجه سانتیگراد حرارت می دهند. پس از اینکه شمش کاملا گداخته شد به صورت مکانیزه به دستگاه های نورد هدایت می شود. تعداد دفعات عبور شمش از دستگاههای نورد به قطر مفتول مورد نیاز بستگی دارد. پس از اینکه مفتول به اندازه ی کافی نورد شد توسط دستگاه های تولید تبدیل به کویل یا توپی مفتول می گردد.
روش خنک کردن محصول به این صورت می باشد که در ایستگاه اولیه نورد حدود 55 درجه سانتیگراد، در ایستگاه های بعد 92 درجه و در ایستگاه نهایی 55 درجه از دمای آن کاسته می شود. با این شرایط در هنگام رسیدن مفتول به ایستگاه پایانی دمایی حدود 980 درجه سانتگراد دارد. اگر میزان افت دما بیش از میزان ذکر شده باشد مفتول پس از نهایی شدن مرحله تولید بسیار ترد و شکننده خواهد شد.
در بازار آهن
در فرآیند سرد شدن شمش گداخته در حال تبدیل به مفتول، دمای 727 درجه سانتیگراد را دمای بحرانی می نامند. در این دما کربن در آهن به صورت فاز پرلیتی شکل می گیرد. فاز پرلیت باعث سخت شدن آهن می گردد. سخت شدن مفتول باعث می گردد برای تولید مفتول کششی با مشکل مواجه گردیم.
در صورتی که در مفتول حفره های گازی مشاهده گردد دلیل آن را در حبس گازهایی که در هنگام شکل گیری و انجماد شمش صورت گرفته است می توان یافت. برای این منظور بهتر است شمش را در خلاء تولید می کنند که این کار مخصوصا در کارخانه های مدرن انجام می شود. از دیگر روش های زدودن حفره های گازی در شمش افزودن آلومینیوم، سیلیسیوم و یا منگنز به مذاب می باشد. این مواد که میل شدیدی به ترکیب با اکسیژن دارند از ایجاد حباب های گازی در مذاب و در نهایت در شمش جلوگیری می کنند.اصطلاح آلومینیوم کیلد یا فولاد نرم شده توسط آلومینیوم از همین فرآیند گرفته شده است.
در صورتی که در فرآیند تولید مفتول پارگی هایی مشاهده گردد، دلیل آن را می توان در ناخالصی های موجود در شمش دانست. این عیب می بایست در هنگام تصفیه فولاد بر طرف شود و بعد از انجماد نمی توان برای آن راهی پیدا نمود. فولاد کثیف به فولادی گفته می شود که ناخالصی های زیادی در هنگام مذاب ریزی داشته باشد. شمش به دست آمده از این مذاب نیز دارای ترک هایی که به صورت چشمی قابل مشاهده هستند می باشد.
بیشتر بدانید :
مفتول کشش
کارخانجات کشش مفتول در زمره صنایع نهایی و پایین دستی صنعت فولاد قرار می گیرند. کششی که در هنگام تولید مفتول کشش صورت می گیرد هیچ گونه تغییری در درصد عناصر شیمیایی آلیاژ مفتول ایجاد نمی نماید. اما تغییرات در خواص مکانیکی و فیزیکی ایجاد می گردد. عمده ترین تغییرات ایجاد شده در مفتول در هنگام عملیات کشش مفتول به شرح زیر است:
- کاهش سطح مقطع
- افزایش طول
- بالا رفتن استحکام کششی
- بالا رفتن تنش تسلیم
عملیات کشش مفتول
بعد از عملیات زنگ زدایی و پوسته گیری، مفتول پس از عبور پودر کشش و دوزه وارد دستگاه کشش می شود. بر اساس نیاز یا کیفیت مفتول یا نوع دستگاه یک یا چند کشش متوالی بر روی آن صورت می گیرد. در اینجا تنش های گوناگون و زیادی بر روی مفتول اعمال میگردد. این تنش ها باعث افزایش طول و کاهش سطح مقطع می گردد. کاهش سطح مقطع بیشتر در مفتول به معنای اعمال تنش بیشتر بر مفتول می باشد و به همین دلیل است که مفتول کشیده شده از مفتول خام سفتتر و دارای چقرمگی بیشتر است. اصولا کار کشش را مانند نوردکاری، چکش کاری و … کارسرد بر روی فلز می نامند و کار سرد باعث سخت شدن فلز و برهم خوردن آرایش اتمی آن می شود و این علت اصلی سفت شدن مفتول در اثر کشش می باشد.
اصولا این سفت شدن در اثر کشش به سه عامل مرتبط می باشد:
- درصد عناصر شیمیایی موجود در مفتول (خصوصا میزان کربن موجود در آن)
- سرعت کشش
- . تعداد دفعات انجام عملیات کشش بر روی مفتول
مراحل کشش مفتول
زنگ زدایی
سطح مفتول در حال تولید در کارخانجات نورد به دلیل اینکه حرارت بسیار بالایی دارد قابلیت اکسید شدن و ترکیب با اکسیژن هوا را دارد. اکسید آهن یک لایه سخت و در عین حال شکننده می باشد. از این رو اولین مرحله در عملیات کشش مفتول، زدودن این اکسیدها و زنگ ها از روی مفتول می باشد که به عمیلات زنگ زدایی موسوم است. یکی از دلایلی که حتما عملیات زنگ زدایی می بایست انجام گردد، آسیب رسانی لایه اکسیدی به قالب های کشش مفتول است.
عملیات زنگ زدایی در چند مرحله و با روش های مختلفی صورت میگیرد که عمده ترین این روش ها عبارتند از:
- زنگ زدایی مکانیکی
- اسیدشویی
- زنگ زدایی مکانیکی همزمان با برس سیمی
- شات بلاست (با فشار ساچمه)
بسته به میزان زنگ زدگی می توان از یک یا چند مراحل بالا بهره گرفت.
عملیات روکش
برخی از انواع مفتول را می بایست پس از تولید با استفاده از فلز دیگری روکش نمود. مهمترین روکش برای مفتول همان فلزِ روی یا Zn می باشد که محصول این روکش کاری تولید می باشد. این روکش به صورت کاملا پیوسته می باشد و دو روش مرسوم برای اعمال روکش گالوانیزه عبارتند از روش گالوانیزه گرم و الکتروگالوانیزاسیون (روش سرد). مفتول پس از گالوانیزه شده مقاومت خوبی به زنگ زدگی پیدا می نماید. از دیگر روکش هایی که بر روی مفتول ها اعمال می گردد می توان موارد زیر را نام برد:
- روکش مسوار
- روکش گالوانیزه
- روکش فسفات روی
در بازار آهن
عملیات آنیل
مراحلی که در کشش مفتول انجام می گردد، به دلیل اعمال نیرو بر روی کریستالهای مفتول باعث ایجاد بی نظمی شدیدی در کریستالهای فولاد به کار رفته در مفتول می شود. این موضوع به اصطلاح کارسختی نامیده می شود. سختی حاصل از عملیات اعمال نیرو بر روی فولاد در اثر ریز شدن دانه ها و در هم ریختن نظم کریستالهای فولاد است. اما در متالورژی برای نظم دادن به کریستالهای فولاد راهی وجود دارد که باعث ایجاد نرمی فولاد و یا از بین بردن اثر سختی ایجاد شده در اثر عملیات مکانیکی می گردد. این روش که از طریق حرارت دادن فولاد و نگهداشتن آن در دما و زمان معینی صورت می گیرد عملیات آنیل نام دارد.
در نتیجه ی انجام عملیات آنیل، خواص انعطاف پذیری، نرمی، قابلیت ماشین کاری و ضربه خواری بهبود پیدا می نمایند. در صورتیکه عملیات آنیل به درستی انجام نگیرد ممکن است باعث ایجاد عیوبی در مفتول گردد. یکی از عیوب متداول در اثر اعمال عملیات آنیل سوختن کربن فولاد و یا به اصطلاح دی کربوره شدن آن می باشد. برای این منظور عملیات آنیل را باید با سرعت 50 تا 100 درجه سانتیگراد در ساعت خنک نمود و در زمانی که دمای کوره به 300 درجه سانتیگراد رسید، کوره را از مفتول تخلیه نمود. اختلاف زیاد در دما و سرعت خنک کردن می تواند موجب بروز عیوب گفته شده در مفتول گردد.
دستگاه دوزه کشش مفتول
در پایان این بحث مختصری در خصوص دوزه کشش یکی از بخش های به کار رفته در دستگاه کشش مفتول صحبت می کنیم. پیش از آن یادآوری می کنیم که عملیات کشش مفتول در جهت کاهش قطر یا تغییر شکل سطح مقطع مفتول صورت می گیرد. طرای دوزه های کشش بستگی زیادی به نوع و جنس مفتولی که باید توسط آنها کشیده شود دارد. در تصویر شماره 3 اجزای اصلی و زوایای مختلف یک دستگاه دوزه کشش به تصویر کشیده شده است.
به صورتی که در تصویر شماره 3 می توان ملاحظه کرد، دوزه کشش از دو جزء اصلی تشکیل شده است. این دو جزء عبارتند از پوسته ی آهنی دوز و هسته دوزه. پوسته آهنی دوزه از جنس آهن معمولی می باشد و جنس هسته اغلب از آلیاژ تنگستن تشکیل می شود. در قسمت هسته چند جز را می توان به طور جداگانه نامگذاری نمود که عبارتند از راهنما، زاویه ورودی، زاویه تماس، استوانه سایز و زاویه خروجی.
معرفی انواع سیم مفتول
سیم مفتول به طور کلی به دو دسته فابریک و غیر فابریک تقسیم می شود:
- سیم مفتول فابریک از کشش و نازک کردن میلگرد تولید می گردد.
- سیم مفتول غیرفابریک از تسمه های فلزی تهیه می شود.
برخی از مفتول ها برحسب کاربرد و جنس مفتول دسته بندی می شوند که شامل:
- سیم مفتول گالوانیزه
- سیم مفتول سیاه (مفتول آرماتوربندی)
- سیم مفتول سفید (سیم گلخانه، سیم قپان، سیم رابیتس، سیم اسکوپ بندی، سیم توری فنس، سیم خاردار)
- سیم مفتول استیل
هر گونه افزایش قیمت داخلی یا بین المللی این فلز تاثیر مستقیمی برا قیمت انواع سیم دارد. از طرفی سیم مفتول مانند سایر محصولات سیم و کابل مشابه عایق پلیمری دارند که در نتیجه نوسانات قیمت مواد اولیه پلیمری به ویژه پی وی سی تغییری در قیمت این محصول ایجاد خواهد کرد. به منظور اطلاع از قیمت انواع سیم مفتولی روکش دار به سایت ما مراجعه کنید.
میسر میکند (شکل 11 بیان گر میزان انعطاف و کشسانی جوش در حین آزمون کششی است).